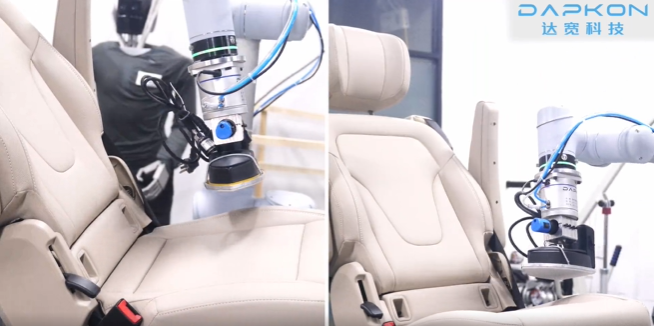
Flexible force-controlled robot seat ironing
In the field of automotive interior manufacturing, the comfort and appearance quality of seats are the focus of consumers. With the advancement of Industry 4.0, the application of automation and intelligent technology is gradually changing the production mode of this industry. Robotic seat ironing technology, as an important part of intelligent manufacturing, is becoming a key technology to improve the quality of seat manufacturing with its high efficiency, precision and safety.
Why is force control needed?
The traditional seat ironing process usually relies on manual work. Workers need to adjust the strength and position of ironing based on experience to make the seat fabric fit fully and the wrinkles flat. However, this method has many limitations:
Inefficiency: Manual operation is slow and labor-intensive.
Unstable quality: Each worker has a different feel, and even the same worker may have inconsistent operating effects at different times.
Safety hazards: High-temperature ironing environment can easily cause worker fatigue or even injury.
In order to achieve more efficient, stable and safe ironing effects, robot ironing has gradually come to the stage. But here comes the problem: even the most advanced industrial robots are difficult to "feel" like human hands. They lack the ability to sense and respond. If they only work according to a fixed trajectory and fixed force, they may not be able to adapt to the complex and changeable shapes of the seat surface, which may easily lead to problems such as uneven ironing and fabric damage.
At this time, the importance of force control technology becomes prominent. By installing a high-sensitivity force sensor at the end of the robot and cooperating with the flexible force control system software, the robot can sense the force changes when it contacts the seat surface in real time, and dynamically adjust its posture and motion trajectory to simulate the "soft" touch and sensitivity similar to that of human hands, thereby achieving high-quality ironing effects.
The force control system software developed by Dapkon integrates high-speed and high-precision dynamic algorithms and control strategies, which enables the robot to automatically adjust its motion trajectory and strength according to the changes in contact force when ironing the seat. The key to this system lies in its "flexibility", that is, it can adapt to different working environments, seat shapes and requirements, achieve more sophisticated and humanized operations, and further optimize the effect of seat ironing.
Dapkon's seat ironing system has the following advantages:
Consistency and repeatability: Through precise force control, the robot can ensure the consistency of each process in different batches of production, keep the ironing effect consistent, avoid errors that may occur in manual operation, and thus improve product quality and brand image.
Product quality traceability: Dapkon's force control system collects data from robots and sensors in real time, and makes each process of ironing each seat cover traceable, which is convenient for quality control and problem tracking. This provides important data support for quality control and subsequent analysis.
Shape adaptability: The shapes of seats are diverse. Dapkon's force control system can detect the changes of seats under subtle forces in real time through precise force sensors, so that the robot can adapt to different geometric structures, adjust the posture and applied force in real time, ensure that ironing covers every corner, and ensure that all indicators of the seat meet the standards.
Flexible force control system software: Dapkon's seat ironing system uses self-developed flexible force control system software, which simplifies the operation process, can adjust the position and posture during ironing in real time, and reduce errors during debugging and operation, making seat ironing easier and more efficient.
As a high-quality supplier dedicated to intelligent flexible robot technology, Dapkon has not only accumulated rich experience in the field of seat ironing, but also actively expanded to collaborative polishing, assembly, gluing, testing and other application scenarios. Dapkon provides customers with one-stop intelligent manufacturing solutions through self-developed flexible control, multi-sensor fusion and AI self-learning technology, combined with deep industry practical experience, to help them solve the pain points of difficult programming and complicated deployment of traditional robots.
In addition, Dapkon's force control system also has real-time data monitoring and consumables management functions, which can monitor and warn the wear of consumables, automatically compensate and protect the robot's end tools, improve the utilization rate of consumables, reduce maintenance costs, and extend the service life of equipment.
Intelligence, flexibility and refinement are important development directions for the future manufacturing industry. The application of Dapkon's flexible force control technology in the ironing process of automobile seats not only greatly improves production efficiency and quality level, but also makes the robot truly "feel" and can complete difficult and demanding tasks like humans. This is not only a technological breakthrough, but also a vivid manifestation of the transformation of the manufacturing industry to intelligence and greenness.
We believe that in the near future, with the continuous iteration and upgrading of technology, the robot flexible force control system will play a greater role in more fields, bringing more innovative value and development momentum to automotive manufacturing and broader industrial fields.
www.dapkon.ai
dapkon
Average Rating