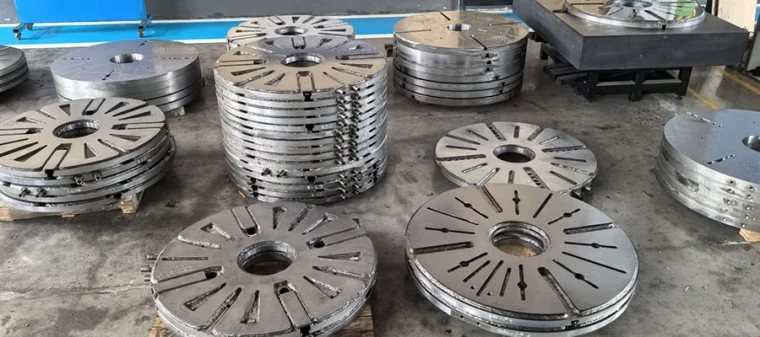
The Role of Hot Press Plates in Modern Manufacturing
In today's fast-paced manufacturing environment, achieving precision, durability, and efficiency in production processes is of paramount importance. Among the various tools and equipment used in industrial production, hot press plates play a vital role in ensuring the quality and reliability of manufactured goods. Hot press plates are widely utilized in industries such as automotive, aerospace, electronics, and more, where high-precision and high-performance components are essential. This blog will explore the significance of hot press plates in modern manufacturing, discussing their applications, benefits, and how they contribute to the advancement of manufacturing processes.
What are Hot Press Plates?
Hot press plates are flat, metallic surfaces that are primarily used in the pressing, molding, or forming processes of materials. These plates are designed to withstand high temperatures and pressures while maintaining structural integrity, making them ideal for applications that require the application of heat and force simultaneously. Hot press plates are typically made from high-quality steel or aluminum alloys, and they are often treated with special coatings to enhance their resistance to wear, corrosion, and extreme conditions.
The plates are used in hot pressing processes, where they are heated to specific temperatures and then applied with controlled pressure to mold or shape materials. This method is commonly used in industries that require precision parts and components with specific mechanical properties, such as hardness, strength, and resistance to wear.
Applications of Hot Press Plates in Modern Manufacturing
Hot press plates are incredibly versatile and are used in various manufacturing applications across multiple industries. Some of the most common applications include:
1. Automotive Manufacturing
In the automotive industry, hot press plates play a crucial role in the production of various vehicle components. They are used in the manufacture of body panels, engine parts, and other critical components that require precise molding and shaping. Hot press plates are particularly important for producing high-strength parts that can withstand the rigorous demands of automotive applications.
For example, in the production of lightweight car body parts, such as doors and hoods, hot press plates are used to mold sheet metal into the desired shapes. The application of heat and pressure ensures that the parts are both lightweight and durable, which is critical for improving fuel efficiency and vehicle safety.
2. Aerospace Industry
The aerospace industry demands parts and components that are lightweight, durable, and capable of withstanding extreme temperatures and pressures. Hot press plates are used in the manufacturing of turbine blades, aircraft fuselage components, and various other aerospace parts. These components often need to be formed from advanced materials, such as titanium alloys and composites, which require precise control over both temperature and pressure during the manufacturing process.
Hot press plates provide the necessary conditions to form complex shapes and geometries from these high-performance materials. The ability to control temperature and pressure precisely is essential for ensuring that the final product meets the stringent performance standards required in the aerospace industry.
3. Electronics Manufacturing
In electronics manufacturing, hot press plates are used in the production of printed circuit boards (PCBs), semiconductor devices, and other electronic components. These parts often require precise thermal management and pressure application during their formation. Hot press plates are essential in processes such as lamination and encapsulation, where materials like copper foils and insulating layers need to be bonded together with high precision.
For example, in the production of multi-layer PCBs, hot press plates are used to bond individual layers of the board together, ensuring that the final product is stable and functional. The plates provide the necessary heat and pressure to create strong bonds between the layers, without damaging the sensitive electronic components.
4. Plastics and Composite Materials
Hot press plates are also extensively used in the production of plastic and composite materials. The hot pressing process is used to mold plastic sheets and composite materials into specific shapes, such as panels, frames, and other structural components. This process is common in industries like construction, automotive, and consumer goods.
For instance, in the automotive industry, hot press plates are used to mold plastic components, such as dashboards, door panels, and bumpers, into their final shapes. The controlled application of heat and pressure ensures that the plastic parts maintain their strength and durability while being molded into complex shapes.
Benefits of Using Hot Press Plates in Manufacturing
The use of hot press plates in modern manufacturing offers several key advantages that contribute to the overall efficiency and quality of production. Some of the primary benefits include:
1. Enhanced Precision and Quality
One of the most significant advantages of using hot press plates is their ability to produce high-precision components. The precise control of both temperature and pressure during the hot pressing process ensures that parts are molded to exact specifications. This is particularly important in industries such as automotive and aerospace, where even minor deviations from the desired shape or mechanical properties can result in costly defects or failures.
2. Improved Material Properties
The application of heat and pressure during the hot pressing process can significantly enhance the material properties of the components being produced. For example, the process can increase the hardness, strength, and wear resistance of materials, making them more suitable for demanding applications. This is particularly important for parts used in industries like automotive and aerospace, where components must withstand extreme temperatures, pressures, and mechanical stresses.
3. Cost-Effectiveness
While the initial investment in hot press plates may be higher than other manufacturing tools, the long-term benefits of using these plates can be substantial. Hot press plates enable manufacturers to produce high-quality components with a high degree of efficiency, reducing the need for rework or scrap. This leads to lower overall production costs and improved profitability.
Additionally, hot press plates are durable and designed to last for many years, making them a cost-effective solution over time. Their ability to withstand harsh conditions and maintain consistent performance reduces the need for frequent replacements or repairs.
4. Versatility and Flexibility
Hot press plates are highly versatile and can be used with a wide range of materials, including metals, plastics, and composite materials. This versatility makes them suitable for various industries and applications, from automotive and aerospace to electronics and consumer goods. Furthermore, hot press plates can be customized to meet specific production requirements, such as varying sizes, shapes, and pressure/temperature specifications.
5. Increased Production Speed
The hot pressing process is relatively fast compared to other methods of molding or shaping materials. This results in increased production speed and higher throughput, which is particularly beneficial for high-volume manufacturing. Hot press plates allow manufacturers to quickly produce large quantities of parts without sacrificing quality or precision, making them an essential tool in modern manufacturing.
Conclusion
Hot press plates play an essential role in modern manufacturing by enabling the production of high-precision, durable, and high-performance components across various industries. Their ability to control both temperature and pressure during the pressing process ensures that parts meet the exacting standards required in sectors such as automotive, aerospace, electronics, and more. With their numerous benefits, including enhanced precision, improved material properties, cost-effectiveness, and versatility, hot press plates will continue to be an indispensable tool for manufacturers in the years to come. As technology advances, the capabilities of hot press plates will only continue to improve, helping manufacturers meet the growing demands for high-quality, efficient production.
How Carburizing Enhances the Durability of Hot Press Plates
www.nuknail.com
Kunshan Liankun Hotplaten Co., Ltd.
Average Rating